Author (Person) | Taylor, Simon |
---|---|
Series Title | European Voice |
Series Details | 26.04.07 |
Publication Date | 26/04/2007 |
Content Type | News |
News, earlier this month, that General Motors, the world’s largest carmaker, was planning to cut 1,400 jobs at its Opel plant in Antwerp, Belgium, was only the latest sign of a trend industry analysts call ‘footprint migration’. Since the birth of the automotive industry, the vast majority of global car and truck production has been located in north America and western Europe. But the wave of restructuring in the automotive industry which has been going on almost continously since the 1970s is being accompanied by an increase in investment in production in eastern Europe and Asia. The global automotive industry faces an ongoing problem of overcapacity, estimated at between 10% and 20% of global annual production according to a survey of automotive industry executives carried out by UK business services company KPMG. In western Europe, the amount of excess capacity is put at between 1.5 and six million cars a year, depending on how overcapacity is calculated. Volkswagen, Germany’s biggest carmaker, is getting rid of 20,000 jobs and Mercedes-Benz is planning to shed 16,000 workers. Staff at the Opel factory in Antwerp downed tools last week in protest at the layoffs. But given that the hourly wages of a west German car worker are roughly three times more than those of someone working at Škoda’s Mlada Boleslav plants in the Czech Republic, what is surprising is that there has not been a greater eastward shift in production away from the high wage plants. Professor Garel Rhys, director of Cardiff Business School’s Centre for Automotive Industry Research, says: "You get the impression from the general press that there’s been a mass exodus." But, he argues, the number of new assembly plants for cars is relatively small while for commercial vehicles it is virtually nothing. Many of the former Communist bloc countries who had domestic truck-making industries have now become export markets for western companies, he points out. The exception is bus-making where Volvo has transferred the major part of its manufacturing into Poland, says Rhys. He calculates that the investment in opening new assembly plants in central and east European countries has only added about 1.2-1.3 million new units to western Europe’s annual output of 15 million new vehicles. New plants include a joint venture between Japan’s Toyota and France’s PSA Peugeot Citroën group, building 300,000 super-minis, including Toyota’s Aygo, at a Czech plant in Kolin. Peugeot has a plant at Tarvan in Slovakia which is scheduled to build 200,000 of its 207 model this year while Korean carmaker Hyundai has opened a new plant in the Czech Republic to build its Kia range. There are a number of explanations for the relatively limited shift in production from west to east. First, the hourly wage differential is not the overriding cost factor as labour charges account for about 10% of the overall cost of assembly of a vehicle and the most efficient plants only require around ten hours of labour per vehicle. Wage costs are of course reflected in the price of components and there has been more of a shift in production of parts to lower wage countries, facilitated by the relatively low cost of transporting small components to assembly plants. Building new assembly plants is a hugely capital-intensive enterprise and many carmakers have chosen to boost productivity at existing plants rather than setting up new ones from scratch. The most productive plants tend to win when carmakers are deciding where to locate production. This was the process that saw Opel’s Antwerp factory lose out when the company announced that its plants in England, Poland, Sweden and Germany would be building the next generation of its Astra hatchback. GM’s plant at Ellesmere Port in north-west England has managed to improve its productivity by around 30% over the last year and further gains are expected thanks to modernisation. Mike Steventon, head of automotive research at KPMG, describes the trend as "footprint rebalancing" rather than outright migration. He estimates that whereas production has been split roughly 85:15 between western and eastern Europe, the proportion could end up 80:20. "It’s not a headlong rush from west to east", he says. Steventon points out that while the shift in production eastwards is limited, investment in eastern Europe is being driven by sales growth in emerging economies. Renault has chalked up a major success with its Logan model, sold under the Dacia brand. Its plant in Romania is producing around 200,000 units a year and the model, with its €5,000 price tag, has become a surprise success not only in the lower prices markets of eastern Europe but also in Germany. But the lower wage advantage of east European states may not last. Workers at Škoda’s Czech plant went on strike to demand a 17% pay increase but finally settled for a pay increase and bonus package worth an extra 13% by 2008. "Wage differentials between east and west will close", says Steventon. He points out that higher wages in eastern Europe will boost demand for vehicles in those countries. Meanwhile, production is increasing further east with companies such as Japan’s Toyota opening plants in Turkey and Russia. For car workers facing the dole queue, such as the GM staff at Antwerp or those at Peugeot’s site at Ryton in the British Midlands, the concept of footprint migration or rebalancing may sound like insidious management double-speak for layoffs, longer hours, worse pay as the car industry shifts eastwards. But the reality is that the vast bulk of production is set to remain in western Europe for years to come. News, earlier this month, that General Motors, the world’s largest carmaker, was planning to cut 1,400 jobs at its Opel plant in Antwerp, Belgium, was only the latest sign of a trend industry analysts call ‘footprint migration’. |
|
Source Link | Link to Main Source http://www.europeanvoice.com |
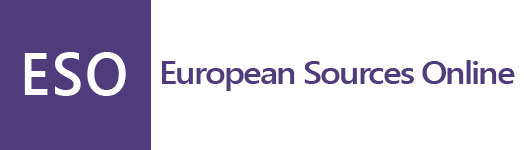